More than half a century of experience
Producer of the original Monoblock®
What we do ourselves, we do better. With this in mind, we took the production process completely into our own hands. As a result, we guarantee the quality and durability of our products as the only producer of composite swimming pools in the Benelux.
- 001
Dutch Design
As a Dutch company, Dutch Design is deeply rooted in our DNA. This is reflected, among other things, in the stylish, clean and minimalist designs of our swimming pools.
- 002
Made in Belgium
As the only manufacturer of composite swimming pools in the Benelux countries, we have full in-house production, giving us complete control over the quality of every aspect of the production process.
- 003
No mass production, but customization
At Starline, we consciously choose customization over mass production. Each pool is made to order according to your specific wishes as a customer. The options are installed in the pool at the factory.
- 004
Outdoor storage? Not at Starline
We deliberately avoid stacked outdoor storage of pools to avoid negative influences of weather factors. Therefore, we transport directly from factory to the desired location.
Monoblock® swimming pools manufactured.
years of experience and expertise.
solar panels installed on our factory.
Step by step to perfection
The production process in steps
Your order has just been received!
Congratulations! You have chosen a pool that perfectly suits all your needs. The pool's specifications, such as colour, size, steps, built-in parts, accessories and techniques, are now being sent to us by your Starline dealer. At our factory, we receive the high-quality raw materials for the Monoblock®, which are stored in specially equipped rooms. Our production moulds are precisely set for the production of your selected Monoblock® model.
Layer by layer
Using production moulds, the Monoblock® is formed layer by layer. The gelcoat applied determines the colour and not only repels groundwater on the outside of the Monoblock®, but also has an antibacterial effect. Then a special Starline resin is applied to the structural layer. The insulation layer is then applied and the bath is provided with a waterproofing outer layer.
Unloading and curing
After applying the layers of the Monoblock®, the pool is unloaded from the mould. The unloading process can take some time due to the unique slope angle of <91 degrees, which requires considerable expertise and time to ensure that no damage is caused to the pool. Once unloaded, the pool is transferred to a special oven for curing. During this curing process, which requires a specific temperature and air circulation, a solid structure is created.
Trimming
After hours in the oven to harden, the Monoblock® goes to the trim booth where the excess materials are manually ground away. This is a precise process that requires skill and experience to get to the desired shape. The result is a perfectly balanced and uniform Monoblock®.
Assembly and quality control
After trimming, the Monoblock® is carefully polished to eliminate any unevenness. The product is then assembled and fitted with specific accessories and components tailored to your specific requirements. This includes the installation of the pipework, the tubular motor of the pool cover, lighting, injectors and skimmers. To complete production, the Monoblock® undergoes a thorough and overall quality check.
Ready for installation
Once the pool meets all quality and safety requirements, it is prepared for shipment. Depending on the agreed installation date, the Monoblock® pool will be stored indoors until it is loaded onto the truck and transported to the site. On site, your Starline dealer will carry out the placement and installation. As the pool is in one piece and already pre-assembled, you can enjoy your new pool quickly and without any worries.
“Every step of the production process is closely measured and controlled. When a pool leaves with us, it is with a guarantee of top quality.”
Jasmin Dolovac, Production Foreman
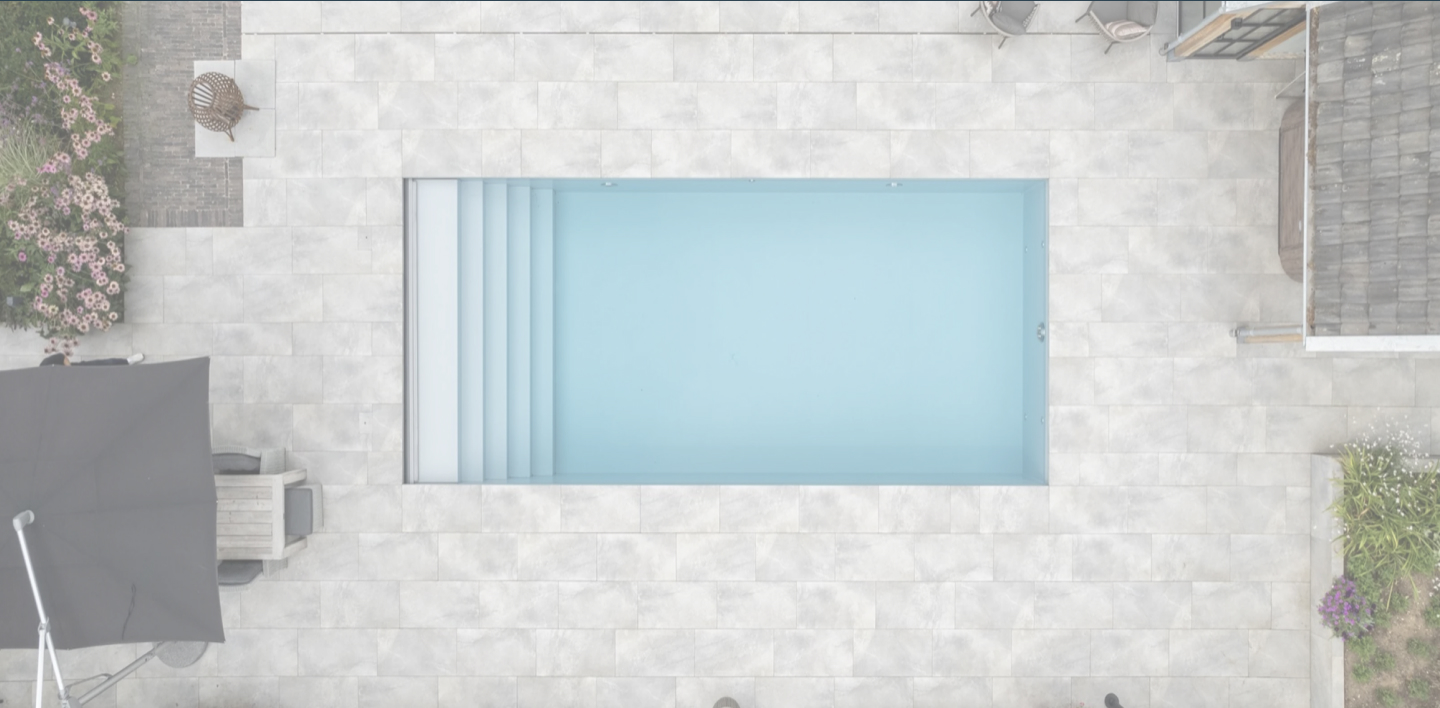
Visit the Starline pool factory
Curious about how your pool is made? We would like to invite you to take a look at our production facility in Pelt (BE), the only pool factory in the Benelux.